Polyurethane
Allgemeine Struktur von Polyurethanen |
![]() |
Wiederholeinheit bei linearen Polyurethanen, die aus einem Diol und Diisocyanat hergestellt wurden. Die Urethan-Gruppen sind blau gekennzeichnet. R1 steht für den „Rest“ des zur Synthese eingesetzten Diols (HO−R1−OH), R2 für den „Rest“ des Diisocyanats (OCN−R2−NCO). |
Polyurethane (Kurzzeichen
PUR; im Sprachgebrauch auch PU) sind Kunststoffe
oder Kunstharze,
die aus der Polyadditionsreaktion
von Dialkoholen (Diolen) beziehungsweise
Polyolen mit Polyisocyanaten
entstehen. Charakteristisch für Polyurethane ist die Urethan-Gruppe
().
Diole und Diisocyanate führen zu linearen Polyurethanen, vernetzte Polyurethane können durch Umsetzung von Triisocyanat-Diisocyanat-Gemischen mit Triol-Diol-Gemischen hergestellt werden. Die Eigenschaften von PU können in einem weiten Rahmen variiert werden. Je nach Vernetzungsgrad und/oder eingesetzter Isocyanat- oder OH-Komponente erhält man Duroplaste, Thermoplaste oder Elastomere. Mengenmäßig sind Polyurethanschaumstoffe, als Weich- oder Hartschaum am wichtigsten. Polyurethane werden jedoch auch als Formmassen zum Formpressen, als Gießharze (Isocyanat-Harze), als (textile) elastische Faserstoffe, Polyurethanlacke und als Polyurethanklebstoffe verwendet.
Geschichte
1937 synthetisierte eine Forschergruppe um Otto Bayer in den Laboratorien des I.G. Farben-Werks Leverkusen zum ersten Mal Polyurethane aus 1,4-Butandiol und Octan-1,8-diisocyanat und später aus Hexan-1,6-diisocyanat. Das entsprechende Polyurethan hatte die Bezeichnung Igamid U bzw. Perlon U. Weitere Versuche zeigten, dass Toluylendiisocyanat deutlich reaktiver war als Hexan-1,6-diisocyanat und dass Reaktionen mit Triolen zu dreidimensional vernetzten Polyurethanen führten. 1940 begann die industrielle Produktion in Leverkusen. Aufgrund des Zweiten Weltkriegs und der damit verbundenen Knappheit an Rohstoffen entwickelte sich der Markt für Polyurethane jedoch zunächst nur sehr langsam. Daher wurden Polyurethane bis Ende des Zweiten Weltkriegs nur für militärische Zwecke im Flugzeugbau verwendet. So waren 1952 weniger als 100 t pro Jahr des wichtigen Polyisocyanats Toluylendiisocyanat (TDI) verfügbar. Von 1952 bis 1954 wurden Polyester-Schaumstoffe entwickelt, wodurch das kommerzielle Interesse an Polyurethanen weiter gesteigert wurde. Mit dem Einsatz von Polyetherpolyolen wuchs die Bedeutung der Polyurethane rasch an. Die größeren Variationsmöglichkeiten bei der Herstellung von Polyetherpolyolen führten zu einer erheblichen Ausdehnung der Anwendungen. So wurden 1960 bereits über 45.000 t an Schaumstoffen produziert.
Bis zum Jahr 2002 ist der weltweite Verbrauch auf rund 9 Millionen Tonnen Polyurethan angestiegen, bis 2007 stieg er weiter auf über 12 Millionen Tonnen. Die jährliche Zuwachsrate beträgt ca. 5 %. 2011 betrug die Produktion allein in Deutschland mit den Hauptproduzenten Covestro und BASF knapp 1 Million Tonnen, davon etwa 32 % für Gebäudedämmung, 20 % für Möbel und Matratzen, 14 % für den Automobilbau und 10 % für Lacke und Farben.
Eigenschaften
Polyurethane können je nach Wahl des Polyisocyanats und des Polyols unterschiedliche Eigenschaften aufweisen. Die Dichte von ungeschäumtem Polyurethan variiert zwischen rund 1000 und 1250 kg/m³. Typische Dichten sind rund 5 bis 40 kg/m³ für weichen Blockschaum oder 30 bis 90 kg/m³ für harten Blockschaum.
- Toxizität
Isocyanate können Allergien auslösen und stehen im Verdacht, Krebs zu verursachen. Wenn Polyurethane ausreagiert sind und keine Monomere mehr enthalten, besitzen sie in der Regel keine gesundheitsschädlichen Eigenschaften mehr. Des Weiteren können dem Polyurethan flüchtige Additive zugesetzt sein, wie Flammschutzmittel oder Weichmacher, die je nach Nutzung dermal (Haut) oder inhalativ (Atmung) aufgenommen werden können. Richtlinien und Merkblätter für den sicheren Umgang mit Polyurethan-Rohstoffen können bei den Herstellern oder der ISOPA (Europäischer Verband der Diisocyanat- und Polyolhersteller) abgerufen werden.
Herstellung
Diisocyanat-Monomere (Auswahl) |
![]() Hexamethylen-1,6-diisocyanat (HDI) |
![]() Toluol-2,4-diisocyanat (TDI) |
![]() Diphenylmethan- 4,4'-diisocyanat (MDI) |
![]() Isophorondiisocyanat (IPDI) |
gängige Diol-Komponenten |
![]() |
![]() |
Polyurethane entstehen durch die Polyadditionsreaktion von Polyisocyanaten mit mehrwertigen Alkoholen, den Polyolen. Die Verknüpfung erfolgt durch die Reaktion einer Isocyanatgruppe (–N=C=O) eines Moleküls mit einer Hydroxygruppe (–OH) eines anderen Moleküls unter Bildung einer Urethangruppe (–NH–CO–O–). Im Gegensatz zur Polykondensation erfolgt keine Abspaltung von Nebenprodukten.
Es kommen nur wenige verschiedene Isocyanatkomponenten zum Einsatz:
- Hexamethylendiisocyanat (HDI)
- Toluylendiisocyanat (TDI)
- Methylendi(phenylisocyanat) (MDI)
- Polymeres Diphenylmethandiisocyanat (PMDI)
- Naphthylendiisocyanat (NDI)
- Isophorondiisocyanat (IPDI)
- 4,4’-Diisocyanatodicyclohexylmethan (H12MDI)
Aufgrund der hohen Flüchtigkeit und der deshalb gefährlichen Verarbeitung kommen von obigen Monomeren in den meisten Fällen bei Verarbeitern nur Präpolymere zum Einsatz, welche allerdings immer einen Restmonomeranteil enthalten. Insbesondere bei HDI ist dies der Fall. Übliche Restmonomeranteile in HDI-Trimerprodukten (z.B. Desmodur N, Tolonate HDT, Basonat oder Duranate) liegen hier bei < 0,5 % HDI und sind damit nach Herstellereinstufung als nicht giftig eingestuft und somit im beruflichen Bereich unter Beachtung der Schutzhinweise der Hersteller verwendbar.
Im Wesentlichen werden die späteren Eigenschaften durch die Polyolkomponente bestimmt, weil zum Erreichen gewünschter Eigenschaften üblicherweise nicht die Isocyanatkomponente angepasst (chemisch verändert) wird, sondern die Polyolkomponente. Abhängig von Kettenlänge und Anzahl der Verzweigungen im Polyol können mechanische Eigenschaften beeinflusst werden. So führt ein Einsatz von Polyesterpolyolen zusätzlich zu den üblicheren Polyetherpolyolen zu besserer Standfestigkeit, weil Polyesterpolyole einen höheren Schmelzpunkt haben und somit beim Applizieren des Polyurethans erstarren.
Die Polyurethanbildung erfordert mindestens zwei verschiedene Monomere, im einfachsten Fall ein Diol und ein Diisocyanat. Die Polyreaktion verläuft in Stufen. Zunächst entsteht aus Diol und Diisocyanat ein bifunktionelles Molekül mit einer Isocyanatgruppe (–N=C=O) und einer Hydroxygruppe (–OH). Dieses kann an beiden Enden mit weiteren Monomeren reagieren. Dabei entstehen kurze Molekülketten, sogenannte Oligomere. Diese können mit weiteren Monomeren, anderen Oligomeren oder bereits gebildeten Polymeren reagieren.
- Polyaddition von 1,6-Hexandiisocyanats mit 1,4-Butandiol (n ≈ 40)
Vernetzungen
Durch einen Überschuss von Diisocyanat können lineare Polyurethane vernetzt werden. Durch Addition einer Isocyanat-Gruppe an eine Urethan-Gruppe bildet sich eine Allophanat-Gruppe.
Durch eine Trimerisierung von drei Isocyanat-Gruppen ist auch die Bildung einer Isocyanurat-Gruppe möglich. Werden mehrfunktionelle Isocyanate eingesetzt, bilden sich die hochverzweigten Polyisocyanurate (PIR).
Alternativ können vernetzte bzw. verzweigte Polyurethane auch durch den Zusatz von Stoffen mit mehr als zwei Isocyanat-Gruppen, wie beispielsweise PMDI, und Triolen, wie beispielsweise Glycerin, hergestellt werden. Auch die Verwendung von mehrfachen Aminen, wie Ethylendiamin, führt zu Vernetzungen. Die Reaktion von Isocyanaten mit Aminen führt erst zu Harnstoff-Gruppen.
Diese sind weiterhin reaktiv und erlauben die Addition einer weiteren Isocyanat-Gruppe, wobei sich eine Biuret-Gruppe bildet.
Soll in der Praxis ein bestimmtes Polyurethan hergestellt werden, so bieten sich zwei Wege an: Die direkte Reaktion eines Polyols mit einem Polyisocyanat (Einstufen-Verfahren) und das Zweistufen-Verfahren. Beim Zweistufen-Verfahren werden im ersten Schritt zwei Prepolymere hergestellt: Mit Diisocyanaten im Überschuss werden bei der Umsetzung mit Diolen ein NCO-Prepolymer und bei einer Umsetzung mit einem Überschuss an Diolen ein OH-Prepolymer gewonnen. Erst im zweiten Schritt erfolgt durch Mischung der Prepolymere die eigentliche Polymerisation. Das Zweistufen-Verfahren führt zu einer sehr weitmaschigen Vernetzung des Polymers und ist für PUR-Weichschaumstoffe wichtig.
Schaumbildung
Wird der Reaktionsmischung eine kleinere Menge Wasser zugefügt, so reagiert Wasser mit Isocyanatgruppen zur entsprechenden instabilen Carbamidsäure, die unter Abspaltung von Kohlenstoffdioxid (CO2) zum Amin zerfällt. Dieses Amin reagiert mit einer weiteren Isocyanatgruppe zum entsprechenden substituierten Harnstoff. Die Freisetzung von CO2 führt daher zu keinem Abbruch der Polymerisation. Das entstehende Kohlenstoffdioxid schäumt die Reaktionsmasse auf.
- Reaktion von Isocyanat mit Wasser unter Entstehung von CO2 und der Bildung einer Polyharnstoff-Gruppe
Durch die Menge des zugegebenen Wassers kann das Raumgewicht des entstehenden Schaumes variiert werden.
Biogene Polyole
Im Regelfall entstammen sowohl die Polyole wie auch die Polyisocyanate der Produktion aus petrochemischen Rohstoffen, es können jedoch auch Polyole auf der Basis von Pflanzenölen oder Lignin eingesetzt werden, siehe Polyole. Als Triol kann Rizinusöl in Beschichtungen eingesetzt werden.
Anwendung
Schaumstoffe
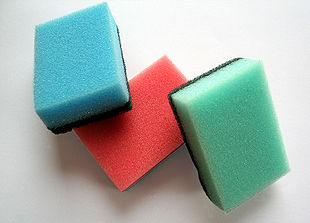
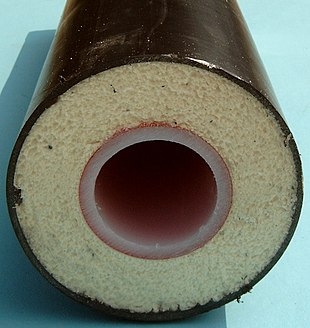
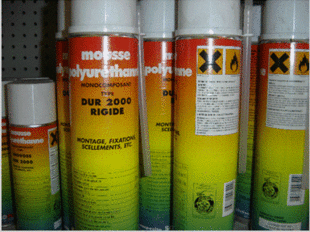
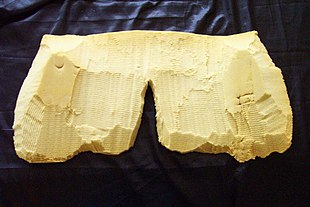
Aus Polyurethan lassen sich sehr einfach Schaumstoffe herstellen. Das Besondere an PUR-Schaumstoffen ist, dass verarbeitende Betriebe Halbzeug (Schaumstoff in zugeschnittener Form) nehmen oder Schaumstoffe aus flüssigen Komponenten an Ort und Stelle herstellen (Ortschaum, „Formed in-place foam“) können. Die Komponenten können auch in oder auf Industrieteile gebracht werden; dort entsteht dann der Schaum.
Weiche PUR-Schaumstoffe werden für sehr viele Zwecke verwendet, vor allem als Polstermaterial (z.B. für Möbel bzw. Autositze) als Matratzenschaum, als Teppichrückenmaterial, zur Textilkaschierung, als Reinigungsschwamm oder als Filtermaterial. PUR-Weichschäume sind zumeist offenzellig und sind in einem breiten Härte- und Dichtebereich verfügbar.
PUR-Hartschäume werden vor allem zur Wärmedämmung z.B. in Gebäuden, Kühlgeräten, Wärme- und Kältespeichern sowie einigen Rohrsystemen (Kunststoffmantelverbundrohr, flexible Verbundrohre) eingesetzt.
Weitere, relativ neue Anwendungsgebiete für PUR-Schäume gibt es im Fahrzeugbau (Lenkrad, Armauflage, Softbeschichtung von Handgriffen, Innenraumverkleidung, Armaturenbrett, Schalldämmung, Klapperschutz, Abdichtungen, Transparentbeschichtung von Holzdekoren).
Polyurethan-Schäume, die als Wärmedämmung konzipiert sind, sind geschlossenzellig aufgebaut, damit die Zellgase mit ihren niedrigen Wärmeleitfähigkeiten in den Schaumzellen verbleiben. Früher kam häufig R 11 (Trichlorfluormethan) als Zellgas zum Einsatz. Wegen der ozonschädigenden Eigenschaft dieses halogenierten Kohlenwasserstoffs wurde dieser weitgehend zunächst durch Kohlendioxid und aktuell durch Cyclopentan ersetzt, wobei dann in den Schaumzellen ein Gemisch aus Cyclopentan (ca. 10 bis 35 %) und Kohlendioxid enthalten ist. Wenn der Polyurethan-Schaum nicht diffusionsdicht gegenüber der Umgebung eingekapselt ist, werden die ursprünglich vorhandenen Zellgase unter irdischen Bedingungen durch Diffusionsvorgänge nach und nach durch Luft und Wasserdampf ersetzt, wodurch die Wärmeleitfähigkeit des Polyurethan-Schaums zunimmt. Nach der Herstellung erreichen Polyurethan-Schäume mit Kohlendioxid als Zellgas Wärmeleitfähigkeiten von ca. 0,029 bis 0,033 W·m−1·K−1, Polyurethan-Schäume mit Cyclopentan als Zellgas Wärmeleitfähigkeiten von ca. 0,022 bis 0,027 W·m−1·K−1. Die Polyurethan-Schäume können sowohl hart als auch flexibel mit unterschiedlichen Dichten eingestellt werden.
PU-Hartschaumplatten sind in verschiedenen Dichten verfügbar. Die Produkte sind teils mit Füllstoffen versehen (Glasmikroballons, Aluminiumpulver). Einsatzzweck sind Dämmstoffe sowie der Modell- und Vorrichtungsbau. Der Schaum wird dazu meist spanend bearbeitet.
Früher wurden Polyurethan-Schaumstoffe mit Pentabromdiphenylether flammgeschützt. Wegen der Toxizität dieses Stoffs kommen heute andere Flammschutzmittel wie beispielsweise TCPP oder Blähgraphit zum Einsatz.
Lacke, Beschichtungen und Klebstoffe
Eine der wichtigsten Anwendungen von Polyurethanen ist der Einsatz in Lacken und Beschichtungen. Hier werden Polyurethane wegen ihrer guten Haftungseigenschaften als Grundierungen und wegen ihrer hohen Beständigkeit gegen Lösemittel, Chemikalien und Witterungseinflüsse als Deck- und Klarlacke in vielen Anwendungsbereichen verwendet. Hierzu gehören z.B. auch Bandbeschichtungs-Lacke und Beschichtungen für Fußböden. Des Weiteren zu nennen sind Textilbeschichtungen und -Ausrüstungen sowie Lederzurichtungen. Flächige Anwendungen zur Verklebung von unterschiedlichen, vorzugsweise flexiblen Materialien (im Bereich Schuhe, Holz/Möbel, Automobilinnenraum) sind ebenfalls ein wichtiges Anwendungsgebiet von Polyurethansystemen. In der Medizin werden Polyurethane als Liner in der Prothetik der unteren Extremitäten verwendet.
Zur Anwendung kommen flüssige Systeme, wie feuchtigkeitshärtende Prepolymere, 2-Komponenten-Systeme, High Solids, Polyurethan-Lösungen und Polyurethandispersionen, aber auch Feststoffe, z.B. Granulate (TPUs) oder Pulver, die aufgeschmolzen oder gelöst werden.
Vergussmassen
- PU-Vakuumgießharze: Verschiedene Produkte mit kurzer Topfzeit, meist für Prototypen oder Vorserien, die z.B. Serienmaterialien (Thermoplast-Spritzguss: ABS, PP, POM, PS, PC, PMMA etc.) ähnelnden mechanischen und thermischen Spezifikationen oder optischen Aspekten entsprechen. Sie werden in einer Vakuumgießanlage verarbeitet. Formen in der Regel aus polyadditionsvernetzendem Silikon. Beispielsweise für die Duplizierung von mit Rapid-Prototyping-Techniken gefertigten Teilen.
- PU-Schnellgießharze: relativ einfach zu verarbeitende Produkte für Gussteile, Modelle und Werkzeuge, die eine kurze Topfzeit besitzen und nicht unter Vakuum verarbeitet werden müssen.
- Elastomer aushärtende PU-Gießharze: Produkte mit verschiedenen im Shore-A- und Shore-D-Bereich angesiedelten Härtegraden. Für elastische bis hartelastische Teile, Formen und Werkzeuge.
- Elektrische Vergussmassen: zum Umgießen/Ummanteln von elektrischen und elektronischen Bauteilen (Potting) zum Zwecke der elektrischen Isolation und dem Schutz vor aggressiven Umgebungsbedingungen (chemisch, Temperatur, Vibrationen, mechanisch)
- Kantenvergussmassen: zum Umgießen /Ummanteln von Holz /MDF. Mit Polyurethan als Kantenvergussmaterial besteht sicherer Schutz vor Schlägen, Kratzern etc. Kantenvergussysteme können lichtecht oder lichtbeständig eingestellt sein. Auch Flammschutz spielt vor allem bei Anwendungen im öffentlichen Personenverkehr eine wichtige Rolle. Die Kantenvergusssysteme sind auch beständig gegen chemische und mechanische Einflüsse.
Spezielle Verwendungen
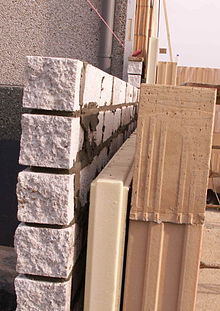
Aus Polyurethan werden Wundauflagen, Matratzen, Schuhsohlen, Dichtungen, Schläuche, Fußböden, Dämmstoffe, Lacke, Klebstoffe, Dichtstoffe, Skier, Autositze, Laufbahnen in Stadien, Armaturenbretter, Vergussmassen, latexfreie Kondome (Präservative), Gussboden und vieles mehr hergestellt.
- In der optischen Industrie wird mit bestimmten Poliermitteln (z.B. Cerdioxid) gefülltes Polyurethan für die CNC-Politur von optischen Funktionsflächen verwendet.
- In der Laborgeräte-Industrie dient Polyurethan als Werkstoff für die Beschichtung von Messkolben. Die Gebrauchstemperatur reicht von −30 bis +80 °C. Kurzzeitige Einwirkungen höherer Temperaturen bis 135 °C sind zwar zulässig, doch führt dies auf Dauer zur Verringerung der Elastizität.
- In der Druck-Weiterverarbeitung werden Buchrücken mit Polyurethan geklebt.
- Polyurethan wird im Bauwesen als 1- oder 2-Komponenten-Schaum (Montageschaum, Expansionsschaum) zum Abdichten von Fugen im Beton vor dem Vergießen, zum Stabilisieren von Fundamenten, zum Anheben von Gebäudeteilen, Fußböden etc. verwendet und beim Einbau von Fenstern und Türen benutzt. Vor allem in den Niederlanden wird es auch als Bodenbelag in Wohnhäusern verwendet.
- Polyurethan-Hartschaum wird als Isolier- und Dämmschicht in Sandwich-Elementen eingesetzt. Die Elemente bestehen aus einem inneren und äußeren Blech (Alu oder beschichtetes Stahlblech), wobei der Zwischenraum durch den aufquellenden PU-Schaum ausgefüllt wird. Überwiegend werden diese Sandwichelemente im Industriebau bei Systemhallen eingesetzt, da sie vorgefertigt werden und auch schnell montiert werden können. So entstehen in kurzer Zeit Wand- und Dachkonstruktionen, die gedämmt und innen wie außen sofort fertig sind. Auch bei gedämmten Roll- und Schiebetoren (Garagentore) werden Sandwichelemente verbaut. Außerdem wird PUR Hartschaum im Kälteschutz verwendet, da dieser Schaum Dampfdiffusion bremst oder verhindert. Üblicherweise werden die Rohre ähnlich wie im Sandwichverfahren mit Blech ummantelt (Edelstahl, verzinkter Stahl, Aluminium, verzinktes Aluminium oder aluminiertes Stahlblech) und anschließend mit dem Zweikomponentenschaum befüllt.
- PU-Elastomer wird häufig für Textilfasern eingesetzt. Diese Fasern bestehen nicht unbedingt zu 100 % aus Polyurethan. Ebenfalls eingesetzt wird Polyurethan als Mikroschaum für atmungsaktive Membranen für Regenbekleidung.
- Aufgrund der hervorragenden mechanischen Eigenschaften eignen sich bestimmte Polyurethane für Anwendungen, die eine hohe Verschleißfestigkeit verlangen. So z.B. beim Transport von Schüttgütern durch Polyurethanschläuche, oder als Schutzschicht in Rohren und Rohrbögen. Auch als Ummantelung für elektrische Leitungen (z.B. Verlängerungsleitungen) wird es eingesetzt, beispielsweise in der verbreiteten Leitung H07BQ-F.
- Ein weiteres spezielleres industrielles Verarbeitungsspektrum findet sich im Prototypen- und Musterbau sowie in der Gießereiindustrie. Hier werden Produkte aus Polyurethan eingesetzt, um Modelle und Werkzeuge vielerlei Art, aber auch Serienteile herzustellen.
- Bei der Herstellung von multifilen Tennissaiten wird Polyurethan als Füllstoff verwendet.
- Moderne Fußbälle (z.B. Roteiro) werden komplett aus Polyurethan gefertigt.
- Der äußere Mantel eines Bowlingballs besteht aus Polyurethan.
- Hochwertige Gummistiefel werden heute ebenfalls häufig aus Polyurethan hergestellt, da diese viel leichter und kälteelastischer sind als solche aus PVC. Außerdem bietet das geschäumte Polyurethan eine weit bessere Isolation gegen Kälte.
- Kondome/Präservative ohne Latex werden aus Polyurethan hergestellt. Diese sind dünner und sollen "gefühlsechter" sein und sind für Personen mit Latex-Allergie gut verträglich. Im Vergleich zu den üblichen Kondomen aus Latex sind sie jedoch oft teurer (Stand Anfang 2011). PUR ist fester, doch weniger weit dehnbar als Latex.
- Als Ummantelung von Silikonimplantaten kommt es immer häufiger zum Einsatz, da das Gewebe sich gut damit verbindet.
- Das erste Serienfahrzeug mit vollständiger Polyurethan-Karosserie ist der Artega GT.
- Für die Herstellung von Halbleiterwafern sind viele Prozessschritte nötig. Um eine ebene Oberfläche zu gewährleisten, werden die Wafer zwischenzeitlich immer wieder poliert (siehe CMP, chemisch mechanisches Polieren). Die Polierplatte besteht dabei in den meisten Fällen aus einem Polyurethan-beschichteten Kunststoff. Für den Abrieb sorgen kleine Polierpartikel, die man zwischen Polierpad und Wafer bringt.
- In der herstellenden Schmuckindustrie wird PU als Einlage für verschiedene Ketten (Hals-, Hand- und Fußkettchen) verwendet, wodurch eine besondere Optik erzielt wird.
- Die Laufflächen von Inlineskate, Skateboardrollen und Laufrollen von Achterbahnen werden aus PU hergestellt, zum Teil auch Tragrollen von Fördergurten und Fließbändern. Das PU bestimmt maßgeblich die Laufeigenschaften der Rollen.
- Lenkgummis (Bushings) von Skateboardachsen bestehen ebenso aus PU.
- Schuhsohlen und Stehmatten im Gesundheitsbereich. Durch PU sind diese weich-elastisch.
- Einer der beiden Bestandteile des Lederimitats Alcantara.
- In der Kosmetik als Bestandteil von Farbkosmetik-, Hautpflege-, Haarpflege- und Sonnenschutzprodukte.
Handelsnamen
- Blockmaterial: Necuron, obomodulan, Ureol, Raku-Tool, RenShape
- Dichtungsmasse: Betamate, Sikaflex, Dymonic NT, Raku Pur
- Fasern: Elastan (Spandex), Lycra, Dorlastan
- Hartschäume: steinothan, BauderPIR, Baytherm, Baydur, Elastolit
- Klebstoffe: Baycoll, Beli-Zell, Desmocoll, Sikaflex, Gorilla Glue, Delo-Pur
- Kosmetik: Baycusan (Mikroplastik)
- Lacke und Beschichtungen: Lupranol, Lupranat, Bayhydrol, Bayhydur, Sikafloor, Desmodur/Desmophen (=DD-Lacke), Voranol, Voranate, Suprasec, Basonat, Sovermol, Tolonate, Duranate
- Membranen: Dermizax
- Polyester-Urethan-Kautschuk: Baytec, Cellasto, Vulkollan, Elasturan, Sylomer, Sylodyn, Urepan, Regufoam
- PU-Folien: Walopur, Walotex, Platilon
- Thermoplastische Polyurethane: Elastollan, Desmopan
- Vergussmassen: Arathane (Elektronik), Baygal/Baymidur (Elektro- und Elektronikvergussmassen), Bectron (Elektronik), Elastocoat, Fermadur, RAKU PUR-Vergussmasse (Elektronik), Stobicast (Elektrotechnik, Elektronik), WEVO-Vergussmasse (Elektronik), Wepuran-Vergussmasse (Elektronik)
- Weichschäume: Bayflex, Elastoflex, Elastofoam, Fermapor K31, Plasthan, RAKU PUR-Dichtungsschaum
Normen
- EN 13165 Wärmedämmstoffe für Gebäude – Werkmäßig hergestellte Produkte aus Polyurethan-Hartschaum (PU) – Spezifikation.



© biancahoegel.de
Datum der letzten Änderung: Jena, den: 04.04. 2025