Verdichter
Verringert man das Volumen eines Gases, so spricht man von Verdichten bzw. Komprimieren. Entsprechende Geräte heißen Verdichter oder Kompressoren.
Bei Verdichtungsvorgängen wird ein vorhandenes Ansaugvolumen
V1 mit dem Betriebsdruck p1 zu einem kleineren Volumen V2 zusammengepresst. In dem kleineren Volumen V2
herrscht ein erhöhter Druck p2,
und das Gas erwärmt sich.
Da sich das Volumen während der Verdichtung verringert, ist es entscheidend, den jeweiligen Druckzustand zum
Volumenstrom anzugeben. Übliche Angaben sind der Saugvolumenstrom (bezogen auf Saugdruck p1),
Austrittsvolumenstrom (bezogen auf den Enddruck p2) sowie der Normvolumenstrom
(bezogen auf den Normzustand
p = 101,3 kPa, T = 273,15 K = 0°C .
Für Verdichtungsvorgänge gilt bei konstant bleibender Temperatur das Boyle-Mariottesche Gesetz.
Verdichter sind Strömungsmaschinen zur Umwandlung
mechanischer Arbeit in Druckenergie.
Eine Verdichterstufe besteht aus Laufrad und Leitrad (vor der ersten Stufe ist häufig noch ein Vorleitrad angeordnet). Der Verdichter kann aus 1
oder mehreren Stufen bestehen. Entsprechend der Strömungsrichtung
unterscheidet man Radial- und Axial-Verdichter.
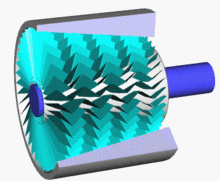
Für Kleingasturbinen und kleine Gasturbinenflugzeuge werden 1 stufige Radialverdichter, sonst vielstufige Axialverdichter verwendet.
Radialverdichter erreichen ein Stufendruckverhältnis von 4 - 5, hochbesastete Axialverdichter großer ZTL 14 - 20.
Wichtige Kennwerte und Daten eines Verdichters sind:
- Wirkungsgrad
- Reaktionszeit
- Laufzahl
- Druckverhaltnis
- Massedurchsatz
- Eigenmasse
- Drehgeschwindigkeit und Durchmesser (Schallgeschwindigkeit beachten!)
Beim Turboverdichter wird durch einen rotierenden Läufer nach den Gesetzen der Strömungsmechanik dem strömenden Fluid Energie zugesetzt. Diese Bauart arbeitet kontinuierlich und zeichnet sich durch geringe Druckerhöhung pro Stufe und hohen Volumendurchsatz aus. Radial- und Axialverdichter sind die beiden Hauptbauarten für Turboverdichter. Beim Axialverdichter strömt das zu komprimierende Gas in paralleler Richtung zur Achse durch den Verdichter. Beim Radialverdichter strömt das Gas axial in das Laufrad der Verdichterstufe und wird dann nach außen (radial) abgelenkt. Bei mehrstufigen Radialverdichtern ist damit hinter jeder Stufe eine Strömungsumlenkung notwendig.
Transsonischer Verdichter
Unter einem transsonischen Verdichter versteht man einen Turboverdichter axialer oder radialer Bauart, in dem die Strömungsgeschwindigkeit im Relativsystem (der Beobachter „sitzt auf der rotierenden Rotorschaufel“) mindestens lokal die Schallgeschwindigkeit übersteigt. Die vorderen Stufen moderner Verdichter in Flugtriebwerken und Gasturbinen sind meist transsonisch ausgelegt, da hier die Temperaturen noch gering sind und man bei gleicher Strömungsgeschwindigkeit eine höhere Mach-Zahl erhält. Die Machzahl ist das Verhältnis der Strömungsgeschwindigkeit zur Schallgeschwindigkeit, letztere ist eine Funktion der Temperatur und der chemischen Zusammensetzung des Gases.
Der Vorteil transsonischer Verdichter sind die hohen Leistungsdichten, was insbesondere bei Flugzeugtriebwerks-Verdichtern wichtig ist, da so das System sehr kompakt ist. Diese Verdichter sind durch komplexe Systeme von Verdichtungsstößen gekennzeichnet, die die Auslegung und den stabilen Betrieb des Verdichters erheblich erschweren. Nachteilig sind auch die hohen Verluste, die mit den Verdichtungsstößen einhergehen und welchen nur durch komplexe dreidimensionale Beschaufelungen und ausgefeilte Profile begegnet werden kann. Üblicherweise sind die ersten Stufen des Niederdruckverdichters bei Triebwerken transsonisch ausgelegt wegen des großen Durchmessers der Rotoren und der Drehzahlgleichheit aller auf der Welle befindlicher Aggregate.
Technisch
Kolbenverdichter
Man unterscheidet Hubkolbenverdichter und Drehkolbenverdichter.
Bei Hubkolbenverdichtern wird das Gas in einem Zylinder von einem hin- und hergehenden Kolben in den Arbeitsraum angesaugt, dort verdichtet und wieder ausgestoßen. Diese Verdichter arbeiten zyklisch, haben geringe Volumenströme und hohe Druckverhältnisse. Ansaug- und Auslassventil sind automatisch arbeitende Plattenventile.
Von den Drehkolben- oder Rotationsverdichtern gibt es verschiedene Bauarten (Roots-Gebläse, Flügelzellenverdichter, Schraubenverdichter, Scrollverdichter). Ihnen ist gemeinsam, dass der Arbeitsraum zwischen dem Gehäuse und einem oder mehreren Verdrängern (Drehkolben) gebildet wird, die sich drehen oder auf eine Kreisbahn bewegen. Angesaugt und ausgestoßen wird das Gas durch Schlitze, die der Kolben bei seiner Bewegung freigibt und verschließt.
Verdichtungsverhältnis
Als Verdichtungsverhältnis
bezeichnet man bei Kolbenmotoren
das Verhältnis des gesamten Zylinderraumes
vor der Verdichtung (Gesamtvolumen)
zum verbliebenen Raum nach der Verdichtung (Restvolumen).
Das Verdichtungsverhältnis darf nicht mit dem Druckverhältnis von Umgebungsdruck zu Kompressionsdruck verwechselt werden. Da mit der Kompression auch die Temperatur steigt, bedeutet ein geometrisches Verdichtungsverhältnis von z.B. 10:1, dass der Druck der eingebrachten Luft auf deutlich mehr als das Zehnfache steigt.
Bei Motoren mit Atkinson- oder Miller-Kreisprozess kann nicht der maximale Zylinderraum als Berechnungsbasis herangezogen werden, weil in der Regel die Einlassventile früher schließen und somit die Zylinderfüllung vorzeitig (vor dem unteren Totpunkt) abgeschlossen wird.
Das Verdichtungsverhältnis kann berechnet werden mit der Formel:
Das Verdichtungsverhältnis von nicht aufgeladenen Benzinmotoren liegt heute bei 10:1 bis 14:1. Aufgeladene Motoren sind niedriger verdichtet. Der maximale Verdichtungsdruck liegt treibstoffbedingt bei 25 bis 30 Bar.
Bei Dieselmotoren ohne Aufladung liegt die Verdichtung bei etwa 19:1 bis 23:1. Aufgeladene Dieselmotoren sind etwa 14:1 bis 16:1 verdichtet. Der maximale Verdichtungsdruck liegt treibstoffbedingt bei 50 bis 60 Bar.
Bei höherem Verdichtungsverhältnis (genauer: Expansionsverhältnis) ist auch
der thermische Wirkungsgrad
höher. Beim idealen Otto-Kreisprozess
ergibt sich der Wirkungsgrad
mit der Verdichtung
und dem Adiabatenexponenten
.
Luft im unteren Temperaturbereich beim Verdichten hat etwa den Wert von 1,4 und
Brenngas im oberen Temperaturbereich beim Expandieren etwa 1,3. Bei
Kreisprozessberechnungen hat der Arbeitstakt (Expandieren) den größten Einfluss.
Die Wirkungsgradberechnung für den Gleichraumprozess
eines zehn zu eins verdichteten Saugmotors
lautet also:
Beim Ottomotor nimmt die Klopfneigung mit der Verdichtung zu. Klopfen kann durch Benzin mit höherer Oktanzahl und durch Verstellen der Zündung nach spät verhindert werden. Moderne Motoren habe Klopfsensoren, die aufkommendes Klopfen erkennen. Sie können den Zündzeitpunkt an die Benzinqualität und an die Motoreigenschaften anpassen.
Einfluss auf die Klopfneigung hat auch die Brennraumform und die Kühlung. Klopfmindernd wirkt auch die Zündung mit zwei oder mehr Kerzen. Die vorzeitige (vor dem oberen Totpunkt) Direkteinspritzung senkt die Verdichtungstemperatur durch Treibstoffverdampfung. Die nachträgliche (nach dem oberen Totpunkt) Einspritzung während der Expansionsphase senkt die maximale Verbrennungstemperatur. Auch Wassereinspritzung senkt die Maximaltemperatur im Brennraum effektiv. Sie kann leistungssteigernd und effizienzsteigernd eingesetzt werden.

Datum der letzten Änderung: Jena, den: 24.02. 2023