Aluminiumlegierung
Aluminiumlegierungen entstehen durch Legieren von Aluminium mit anderen Metallen, vorwiegend Mangan, Magnesium, Kupfer, Silicium, Nickel, Zink und Beryllium. Als Basismaterial dient in den meisten Fällen Al99,5 (EN AW-1050A). Auf diese Weise lassen sich die Festigkeitswerte in weiten Grenzen erhöhen und auch andere Eigenschaften beeinflussen.
Je nachdem, ob die gewünschte Festigkeitssteigerung nur durch Legierungselemente sowie Kaltverfestigung oder aber vornehmlich durch eine Aushärtebehandlung (Wärmebehandlung) erreicht wird, unterscheidet man zwischen den aushärtbaren und den nichtaushärtbaren (naturharten) Legierungen.
Eine weitere Unterscheidung ergibt sich aus der Art der Verarbeitung: Knet- oder Gußwerkstoffe. Zu den Knetwerkstoffen zählen außer Reinst- und Reinaluminium im wesentlichen die naturharten Legierungen vom Typ AlMn, AlMg und AlMgMn sowie die aushärtbaren Legierungen der Gattungen AlCuMg, AlCuSiMn, AlMgSi, AlZnMg und AlZnMgCu. Sie werden zu Halbzeugen in Form von Bändern, Blechen und Ronden, Rohren, Stangen und Drähten, Strangpreßprofilen sowie Schmiedestücken verarbeitet. Zu den Gußwerkstoffen gehören die Legierungen der Gattung AlSi, AlSiMg, AlSiCu, AlMg, AlMgSi, AlCuTi, AlCuTiMg.
Aluminiumknetlegierungen
Als Aluminiumknetlegierung werden alle Aluminiumlegierungen bezeichnet, welche vor allem durch Umformen (Walzen, Strangpressen) bearbeitet werden.
Bereits geringe Zusätze der Legierungselemente Magnesium, Silicium, Kupfer, Zink, Nickel und Mangan ändern sehr stark die Eigenschaften des reinen Aluminiums. Insbesondere werden Festigkeit und Härte gesteigert, die elektrische Leitfähigkeit gesenkt, während die Umformbarkeit nur gering nachlässt. Diese Legierungen zeigen eine hohe Duktilität, man nennt sie deshalb Aluminiumknetlegierungen. Aluminiumknetlegierungen werden aufgrund ihrer hohen Festigkeit und geringen Dichte als Werkstoffe für Transportbehälter sowie Konstruktionsteile im Fahrzeugbau, Flugzeugbau, und Schiffbau verwendet.
Aluminiumknetlegierungen werden in der Regel statt mit ihrer Werkstoffnummer mit einem von der Aluminum Association erstellten vierstelligen Zahlensystem bezeichnet. Dabei gibt die erste Ziffer das Hauptlegierungselement und damit die Legierungsgruppe an. Die restlichen Ziffern sind mehr oder weniger Zählnummern, die chronologisch oder in Anlehnung an bereits bestehende Legierungen vergeben werden.
Gruppe | Hauptelement | Härtbarkeit | Festigkeit in N/mm2 |
Bemerkungen |
---|---|---|---|---|
1xxx | mind. 99 % Aluminium | naturhart | 70 - 190 | auch Reinaluminium genannt; schweißbar; sehr korrosionsbeständig; Verwendung für Aluminiumfolie, chemische Tanks und Rohre; hohe elektrische Leitfähigkeit. |
2xxx | Kupfer | aushärtbar | 190 - 570 | 0,7 bis 6,8 % Cu - Verwendung in Flugzeug und Raumfahrt - hohe Festigkeit - großer Temperaturbereich. Manche Legierungen gelten aufgrund der Rissneigung beim Schweißen als nicht schweißbar - Schweißzusatz meistens 2xxx, manchmal auch 4xxx. |
3xxx | Mangan | naturhart | 100 - 350 | hohe Korrosionsbeständigkeit - gute Formbarkeit - geeignet auch für höhere Temperaturen - Einsatzgebiet von Kochtöpfen über Kühler in Fahrzeugen (hier oft mit 4xxx plattiert) bis zum Kraftwerksbau. Schweißzusatz 1xxx, 4xxx und 5xxx. |
4xxx | Silicium | aushärtbare und naturharte Legierungen | 170 - 380 | 0,6 bis 21,5 % Si - einzige Serie, die aushärtbare und nicht aushärtbare Legierungen enthält - für die Aushärtung> ist zusätzlich die Anwesenheit von Magnesium erforderlich. Silicium reduziert den Schmelzpunkt und macht die Schmelze dünnflüssiger - ideal für Schweiß- und Lötzusätze. |
5xxx | Magnesium | naturhart | 100 - 450 | 0,2 bis 6,2 % Mg - höchste Festigkeiten unter den nicht aushärtbaren Aluminiumlegierungen - schweißbar - Verwendung im Schiffbau, Transport, Druckkessel, Brücken und Gebäuden. Schweißzusatz muss nach Magnesiumgehalt bestimmt werden. Aluminium aus dieser Serie mit mehr als 3,0 % Mg ist für Temperaturen über 65° nicht geeignet (Spannungsrisskorrosion) - Materialien mit weniger als ca. 2,5 % Mg können oft erfolgreich mit 5xxx oder 4xxx Schweißzusätzen geschweißt werden. 5032 wird meist als das Material mit dem höchsten Mg-Gehalt genannt, das gerade noch mit 4xxx schweißbar ist. |
6xxx | Magnesium und Silicium | aushärtbar | 100 - 450 | Si und Mg um die 1 % - sehr beliebt bei Schweißkonstruktionen - Verwendung vorwiegend als Strangpressprofile - kann gut wärmebehandelt werden - sollte nicht ohne Schweißzusatz geschweißt werden (Warmrisse) - Schweißzusätze 4xxx und 5xxx. |
7xxx | Zink | aushärtbar | 220 - 700 | 0,8 bis 12,0 % Zn - Verwendung in Flugzeugbau, Raumfahrt, Sportgeräte; manche Legierungen sind nicht mit Lichtbogen schweißbar; Legierungen 7005 und 7020 sind gut mit 5xxx-Schweißzusätzen schweißbar, da diese beiden Legierungen kein Kupfer enthalten; |
8xxx | andere Elemente | unterschiedlich | unterschiedlich | z.B. Aluminium-Lithium-Legierungen der ersten Generation. |
Aufstellung typischer Aluminiumlegierungen, die in der Industrie Verwendung finden:
- Aludur (0,3 - 1 % Silicium, 0,3 - 0,8 % Mangan und 0,5 - 1,2 % Magnesium)
- Aluman (1,1 % Mangan)
- Duraluminium (2,5 - 5,5% Kupfer, 0,2 - 5 % Magnesium, 0,5 - 1,2 % Mangan und 0,2 - 1,0 % Silicium)
- Hydronalium (3 - 12 % Magnesium, 0,2 - 0,8 % Mangan und 0,2 - 1,0 % Silicium)
- Silumin® (bis 14 % Silicium)
Aluminiumgusslegierungen
Für Gusslegierungen gilt folgende Einordnung:
- 1xx: Reinaluminiumqualitäten
- 2xx: Kupfer
- 3xx: Silicium-Kupfer/Magnesium
- 4xx: Silicium
- 5xx: Magnesium
- 7xx: Magnesium-Zink
- 8xx: Zinn
Die wichtigste Aluminium-Gusssorte ist die eutektische Legierung von Aluminium und Silicium. Ihr Eutektikum liegt bei etwa 12 % Silicium und hat einen Schmelzpunkt von 576° Celsius. Diese Aluminium-Silicium-Legierung besitzt hervorragende Gießeigenschaften (Dünnflüssigkeit, geringe Schwindung) und hat hohe Festigkeit. Sie lässt sich im allgemeinen gut schweißen und ist korrosionsbeständig. Anteile an Magnesium und Kupfer erhöhen die Festigkeit, Kupfer verringert jedoch die Korrosionsbeständigkeit.
Aluminiumgusslegierungen mit diesen Elementen werden als Werkstoffe beispielsweise für Motorengehäuse und Getriebegehäuse im Fahrzeug- und Flugzeugbau verwendet.
Anwendungen
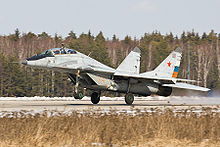
Luft- und Raumfahrtlegierungen
Aluminium-Scandium
Durch den Zusatz von Scandium zu Aluminium entstehen nanoskalige Al3Sc-Niederschläge, die das übermäßige Kornwachstum in der Wärmeeinflusszone von geschweißten Aluminiumbauteilen begrenzen. Dies hat zwei vorteilhafte Effekte:
- Das ausgefällte Al3Sc bildet kleinere Kristalle als in anderen Aluminiumlegierungen und die Breite der ausscheidungsfreien Zonen, die normalerweise an den Korngrenzen von aushärtbaren Aluminiumlegierungen vorhanden sind, wird verringert.
- Scandium ist auch ein wirksamer Kornverfeinerer in Aluminiumgusslegierungen und Atom für Atom der wirksamste Verfestiger in Aluminium, sowohl als Ergebnis der Kornverfeinerung als auch der Ausscheidungsverfestigung.
Ein zusätzlicher Vorteil von Scandium-Zusätzen zu Aluminium besteht darin, dass die nanoskaligen Al3Sc-Präzipitate, die der Legierung ihre Festigkeit verleihen, bei relativ hohen Temperaturen (~ 350 ° C) vergröberungsbeständig sind. Dies steht im Gegensatz zu typischen handelsüblichen 2xxx- und 6xxx-Legierungen, die bei Temperaturen über 250 ° C aufgrund der raschen Vergröberung ihrer festigenden Niederschläge schnell an Festigkeit verlieren.
Mit Scandiumzusätzen verstärkte Aluminiumlegierungen sind im Prinzip den herkömmlichen Superlegierungen auf Nickelbasis sehr ähnlich , da beide durch kohärente, vergröberungsbeständige Niederschläge mit einer geordneten L12-Struktur verstärkt werden. Al-Sc-Legierungen enthalten jedoch einen viel geringeren Volumenanteil an Präzipitaten, und der Abstand zwischen den Präzipitaten ist viel geringer als bei ihren Gegenstücken auf Nickelbasis. In beiden Fällen ermöglichen die gegen Vergröberung beständigen Niederschläge jedoch, dass die Legierungen ihre Festigkeit bei hohen Temperaturen behalten.
Die erhöhte Betriebstemperatur von Al-Sc-Legierungen hat erhebliche Auswirkungen auf energieeffiziente Anwendungen, insbesondere in der Automobilindustrie. Diese Legierungen können dichtere Materialien wie Stahl und Titan ersetzen , die in Umgebungen mit 250 bis 350 ° C verwendet werden, z. B. in oder in der Nähe von Motoren. Der Ersatz dieser Materialien durch leichtere Aluminiumlegierungen führt zu Gewichtsreduzierungen, die wiederum zu einer erhöhten Kraftstoffeffizienz führen.

© biancahoegel.de;
Datum der letzten Änderung: Jena, den: 02.02. 2024